ISO 9001:2015
Our services
Get Started Today
Start your journey with us today – simple, fast, and reliable services.
Download Company
Profile
Download PDF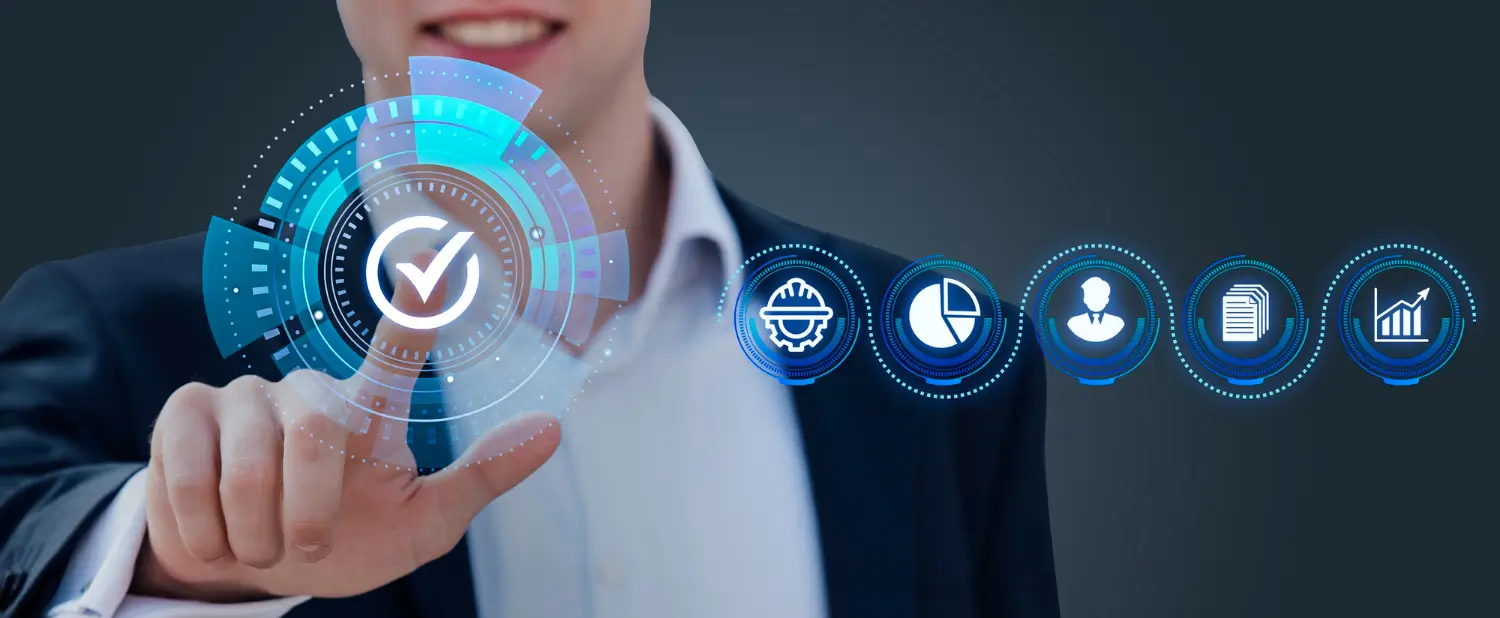
BASIC INTRODUCTION OF QUALITY MANAGEMENT SYSTEM: ISO 9001:2015
ISO 9001 is defined as the international standard that specifies requirements for a quality management system (QMS). Organisations use the standard to demonstrate the ability to consistently provide products and services that meet customer and regulatory requirements. It is the most popular standard in the ISO 9000 series and the only standard in the series to which organisations can certify. ISO 9001 was first published in 1987 by the International Organisation for Standardisation (ISO), The current version of ISO 9001:2015 was released in September 2015 in accordance with ISO 19011. It presents fundamental management and quality assurance practices that can be applied by any organisation. The requirements represent an excellent foundation of planning, control, and improvement for just about any enterprise. Without a QMS, organisations have little chance of sustaining any improvements or innovations they might realise.
HISTORY OF ISO 9001
The present version of ISO 9001 ISO 9001:2015 is the fifth iteration of the standard. Here is a brief history of ISO 9001 through the years: ISO 9001:1987. The first publication of ISO 9001. Truly a manufacturing standard and very heavily focused on documentation. The requirements were based on U.S. military standards used by government contractors since World War II. ISO 9001:1994. A minor revision to the standard. Still very prescriptive and focused on manufacturing. Difficult for services providers to interpret and apply. ISO 9001:2000. A significant revision of the standard with a focus on continuous improvement, customer satisfaction, leadership, and process management. An attempt to make the standard more applicable to service providers, and to make it more flexible in general. ISO 9001:2008. A very minor revision with only slight changes in wording. No actual requirements were added, removed, or changed. ISO 9001:2015. A significant revision to the standard and another step away from its manufacturing origins. Much more of a model for managing and improving an organisation, with risk lying at the heart of the standard. An excellent framework for long-term success and customer satisfaction.